
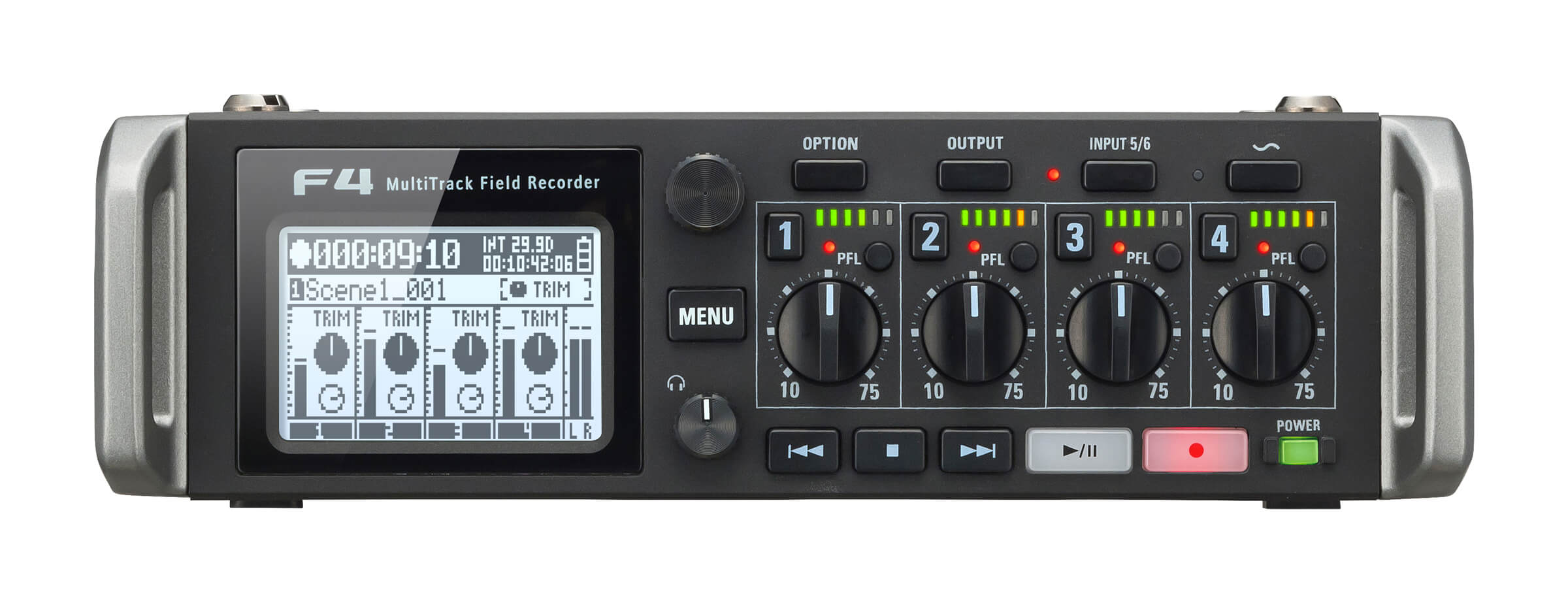
It's nice but I need to get some justification first before I can purchase one for me here. Both FreeWRL and Stereo2 offer excellent frame rates for environments containing points and lower frame rates for (smaller) populations of spheres. For spheres, we measured 1.7 fps for FreeWRL and 15 fps for Stereo2. I do have a 3Dconnexion space navigator mouse I use at home. (fps) for FreeWRL, and more than 100 fps for Stereo2. I least that's what I would have thought? If it's a small error in ball diameter then it looks to me like it may not be noticable, and any large error would probably be seen by the user in FPX or the 2D view of the footprint in the CAD program first. Rotating, panning and zooming are the basic view. z3 : theorem prover from Microsoft Research zoom : Zoom Cloud Meetings.

#Freewrl zoom code
EAI libraries of FreeWRL, which are written in Java, into native code with. the interactive inspection (rotate/pan/zoom), where the user interaction moves. freewrl : X3D/VRML browser fritiof7-dev : Physics Fritiof library (static) from. In future maybe Scan3D will be able to use a photo of the background to better distinguish the profile of the object. Other suggestions Scan3D needs the profiles of the object for many different angles. I'm not sure how you can visually validate the footprint to ensure solder joint accuracy here since the user is probably going to be outputting the 3D model and the footprint from FPX at the same time so if they've an error input values then it's probably going to be a wrong pitch which would be same on both model and footprint, or the wrong ball diameter. users head gaze triggers a zoomed display of the currently observed item. To reduce prospective-effects you should put your camera far from the object and use the zoom to avoid too small images.

Pulsonix has a built in 3D viewer in addition to the STEP file preview and output and in Pulsonix I mainly use the built in 3D viewer for a quick check because the STEP file takes longer.
